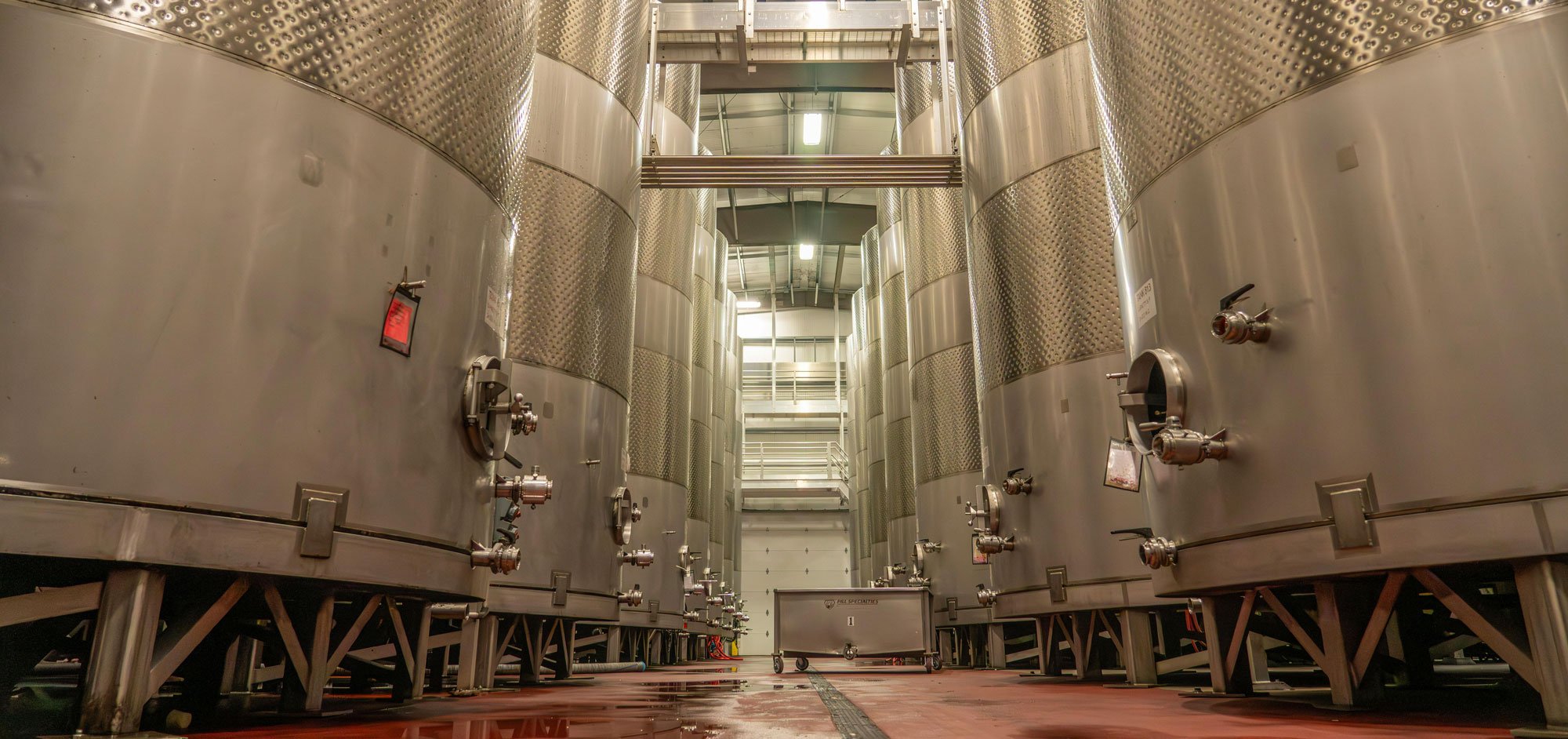
What is a Process?
OSHA defines a “process” in 40 CFR §68.3 as “any activity involving a regulated substance, including any use, storage, manufacturing, handling, or on-site movement of such substances, or combination of these activities. Any group of vessels that are interconnected, or separate vessels that are located such that a regulated substance could be involved in a potential release, is considered as single process.”
This sounds very comprehensive and all-encompassing, but is also worth a critical review to clarify a few points. Since each process is evaluated to determine what level of program is required, it’s really important to define where your process starts and stops, and whether the regulated substance exceeds the threshold quantity level. Let’s consider two similar systems below: In Figure 1.1, the three storage tanks are interconnected. Even though there may be valves that remain closed unless there’s a need to bypass, the fact that product COULD travel between tanks and processes means that this will be considered a single process and the inventory of each tank/process will need to be added to determine program level required.
In contrast, let’s now review Figure 1.2, the tanks are no longer interconnected, and there’s no cross-over for the subsequent processes. If the tanks and processes are sufficiently separated that a release from one would not impact the others, these can now be treated as three separate processes. Why does this matter? If the threshold quantity in the example shown were 10000 pounds, Figure 1.1 would require development and ongoing management of the full PSM program (3 x 4000 lbs = 12000 lbs), where Figure 1.2 would be exempt from the full program, and could be instead managed under General Duty.
Now let’s consider an example of a bottling line that can flex between high-proof spirits and a lower-proof mixed beverage. Spirits are often considered a covered chemical when the components or mixture are flammable (<100°F flash point). When the line is producing the mixed beverage as shown in Figure 2.1, the high-proof spirit portion of the process may stop at the blending step. If the same bottling line is bottling a high-proof spirit as shown in Figure 2.2, the process may extend all the way to the filling step. If a single production line can flex between these two products, all the equipment within the high-proof pathway will need to meet your covered process program requirements for flammable liquids (see RAGAGEP).
While PSM and RMP regulations differ on things such as flammable classifications, filing requirements, and chemical-specific threshold quantities – they all require documentation of the maximum intended inventory for each process. A thorough applicability review of your process(es) including documentation of the calculations used is the best way to both ensure you are following the correct regulations and insulate you from regulatory risk.